Pingxiang Volmet Import&Export Trading Co., Ltd. 萍乡市沃美特进出口贸易有限公司

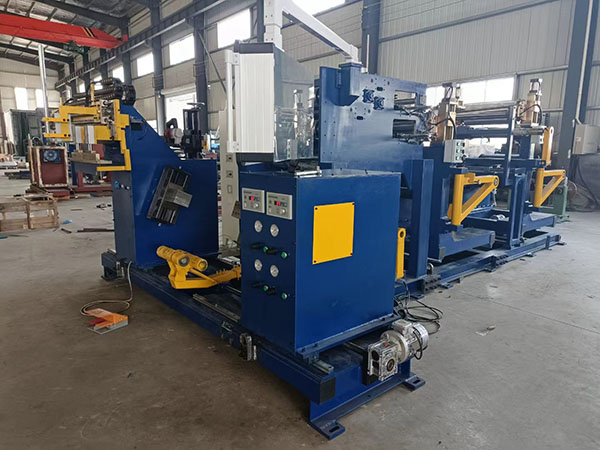
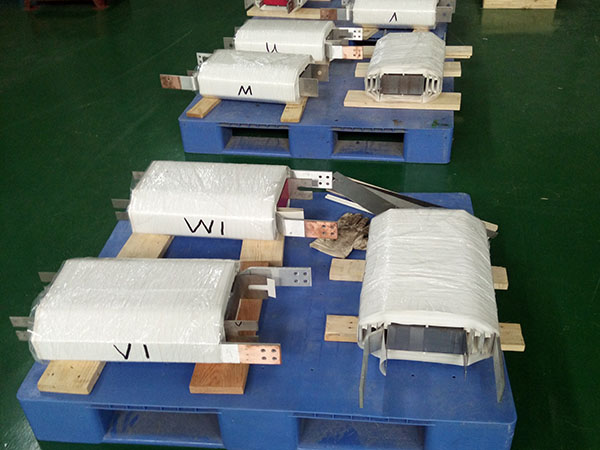
Double Servo Double Layer Copper Foil Winding Machine
Short Description:
Contact Us
1. Use Of Machines
VOL -400-2/600-2/800-2 double servo double clamping foil winding machine produced by the company is a special equipment for winding reactor coils. The machine is a push-button type, with simple structure, easy operation and high reliability, which is the best equipment for winding reactor coils.
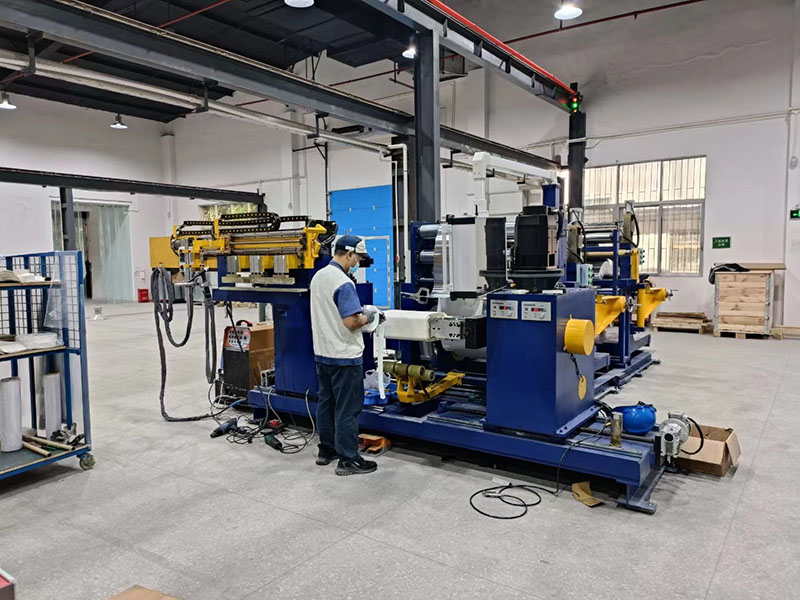
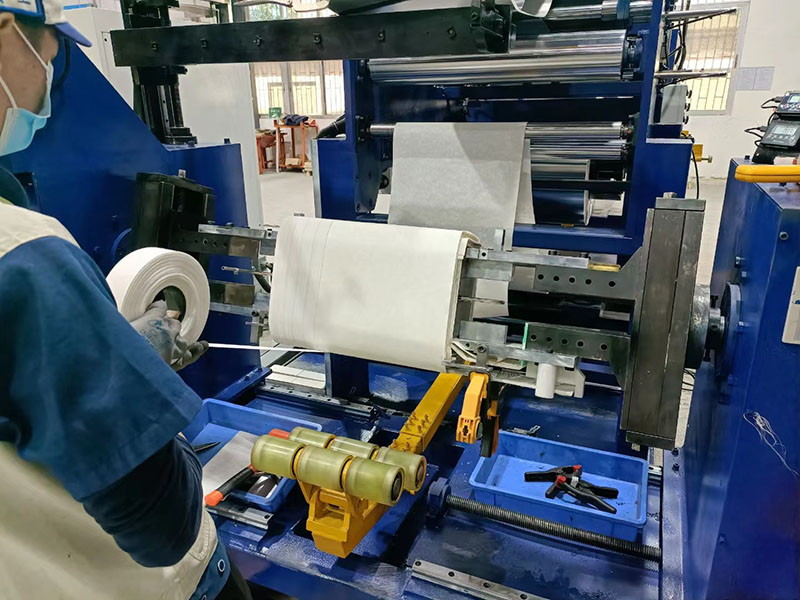
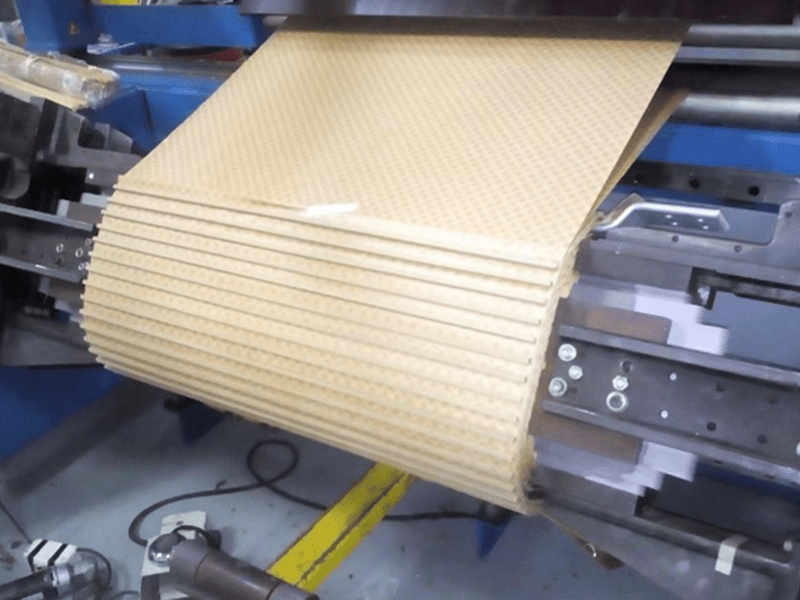
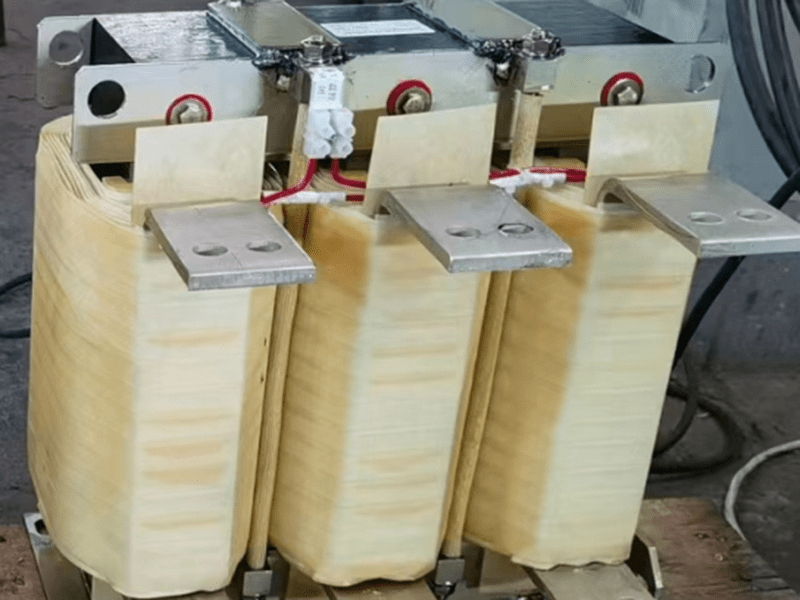
2. Main Technical Parameters Of The Machine
foil winding machine technical parameters |
||||
VOL -400-2 |
VOL -600-2 |
VOL -800-2 |
||
Order no. |
project |
Technical reference number |
||
1 |
Coil working range | |||
1.1 |
The foil material width | 50-400mm | 50-600mm | 50-800mm |
1.2 |
The material | Copper/aluminum foil hickness0.1-2.0mm | Copper/aluminumfoil hickness0.1-2.0mm | Copper/aluminumfoil hickness0.1-2.0mm |
2 |
Foil feeding ( 2 Set of ) | |||
2.1 |
Uncoiler motor power | 3000Nm Tension motor
*2 |
6000Nm Tension motor
*2 |
8000Nm Tension motor
*2 |
2.2 |
Effective width of rack mm | 450mm | 650mm | 850mm |
2.3 |
Increases and the scope of | Ø460~ Ø 520 (mm) | Ø460~ Ø 520 (mm) | Ø460~ Ø 520 (mm) |
2.4 |
Rack bearing(Max)kg | 1T | 2T | 2.5T |
2.5 |
When tight force | 2500Nm*2 | 4500Nm*2 | 6500Nm*2 |
2.6 |
Pressure of work | 0~0.7 Mpa | 0~0.7 Mpa | 0~0.7 Mpa |
2.7 |
On the way | (Move the left and right knobs) | (Move the left and right knobs) | (Move the left and right knobs) |
3 |
Coiler (2 sets) one set left/one set right | |||
3.1 |
Wind speed | 0~30r/min | 0~30r/min | 0~30r/min |
3.2 |
Work torque(Max) | ≥1560N.M*2 | ≥1560N.M*2 | ≥1560N.M*2 |
3.3 |
Wind power | Double servo4KW*2 | Double servo5KW*2 | Double servo7.5KW*2 |
3.4 |
Speed way | Digital control of motor speed | Digital control of motor speed | Digital control of motor speed |
4 |
Fixtures and fittings (2 sets) | |||
4.1 |
Minimum fixture range | 10mm | 10mm | 10mm |
4.2 |
Maximum range of fixture | 350mm | 350mm | 350mm |
4.4 |
The width of the jig | 180mm | 180mm | 180mm |
5 |
Layer insulation device (2 sets) | |||
5.1 |
Insulated motor power | 0.37KW*2 | 0.37KW*2 | 0.37KW*2 |
5.2 |
tension | pneumatic | pneumatic | pneumatic |
5.3 |
Insulating paper width | 100-450mm | 100-650mm | 100-850mm |
6 |
Electric control system | |||
6.1 |
Encoder count | (0-9999.9) | (0-9999.9) | (0-9999.9) |
7
|
Automatic welding (1 set) | |||
7.1 |
Welding width | 400mm | 600mm | 800mm |
7.2 |
Theweldingmachine power | Ac/DC 315 | Ac/DC 315 | Ac/DC 500 |
8 |
The transmission way | Linkage and manual | ||
9 |
Operating mode | Control box |
3.The Machine Is Briefly
VOL -400 double servo double-layer clamping foil winding machine is composed of: base, unwinding transmission box, layer insulation, winding box, control box, etc. The functions of the main components are briefly described below
Uncoiling device: It includes uncoiling transmission box, bracing plate, rectifying motor, etc. As the uncoiling mechanism of foil belt, it has the functions of supporting material reel, uncoiling material releasing, and electric adjusting deviation, etc.
The uncoiling mechanism has a spindle directly from the inside to the center of the external support plate. On the spindle is an outer sleeve connecting the opening and closing of 4 groups of support plates. The center is a screw, which can support the coil material on the feeding barrel. The main shaft can be operated actively in forward or reverse direction for uncoiling and discharging, which is convenient to adjust the working condition at any time. In linkage, the spindle is separated from the driving device by the action of the clutch. The main shaft is equipped with a press roller device, which can be used separately or in parallel. The press roller is pneumatic, which is easy to control and safe.
Rectifying deviation adopts linear guideway, which is equipped with electric power motor, and the button on the control box is adjusted. The unwinding mechanism will move quickly and accurately along the linear guideway, so as to ensure the foil belt is in an accurate position and realize the function of foil belt rectifying deviation.
Winding device: ncludes reduction gear, clamping device, tailstock device;
The winding machine and tailstock device adopt the same winding;
The coiling machine is located in the left front of the equipment, and the output torque is clamped by the clamping device for the core winding. The mechanical strength and output torque of the coiling machine is the optimal consideration in the design. The design is based on the maximum size of the workpiece and the upper limit of the tightening force required by the process, adding enough margin configuration;
The rewinding drive box is composed of thick steel plates welded together, annealed to remove stress and processed by high-precision machining. Transmission mode: the reducer is used to drive, which ensures the mechanical strength and the overall smooth operation of the equipment and the extremely low working noise when large torque is output.
Adopt the servo digital speed regulation mode, through the input number, the low speed section provides the maximum torque, the appropriate speed. To meet the requirements of different winding process. Equipped with braking function, improve the operation of the equipment, the use of motor driven, abundant reserve power.
Layer insulation device: The layer insulation device is a mechanism that supports the coil of insulating material and causes the insulating material to generate swelling force while winding and receding.
The mechanism is composed of four parts, namely, air swelling shaft, bracket, driving system, pneumatic coupling, etc. Increase force pressure, clutch increase force, small, so that the layer insulation in the winding and back process to maintain the increase force state.
Electronic control system: Mitsubishi PLC, control box and button operation are adopted in Japan. Different instructions are given after winding through PLC control system operation, which is implemented by each system. Operators only need to input relevant working parameters in the counter, it is convenient to complete the mass production of the same specifications of the workpiece. Each device can also be operated manually through the control button, including inching, linkage, etc. An emergency stop button is set at the main console position and the main device to stop the machine in time in case of any abnormality, so as to ensure safety.